Model No.: PRMC-003A
Machining Process: Turning, Milling, Bending, etc.
Surface Treatment: Anodized, Sandblast, Powder Coating
Color: Red, Black, Blue, Yellow, Silver
Samples Offer: Available
Shipping Way: DHL, FedEx, UPS, or by Sea
Trademark: PREMIUM
Transport Package: Multiplayer Wood Box/Pallet with Big Plastic Bag
Specification: Customized
Origin: Shenzhen, China
HS Code: 848190900
Product DescriptionÂ
Material |
Aluminum (6061-T6, 6063, 7075-T6, 5052) etc... Brass/Copper/Bronze etc... Stainless Steel (302, 303, 304, 316, 420) etc... Plastic (ABS, PP, PE, PC) etc... |
Process | CNC Machining, CNC Turning, CNC Milling, CNC Lathe, CNC Boring, CNC Grinding, CNC Drilling etc... |
Quality Assurance | ISO9001:2008 Certified, SGS Certification |
Surface Treatment |
As Machined; Sand Blasting; Powder Coating; Smooth Finish; Anodizing; Chrome Plating; Gloss or Matt Color; and Many More Custom Coatings & Finishes |
MOQ | 1 piece |
Lead Time | 5–10 working days |
Packaging | Carton Box / Wooden Case |
Term of Payment | T/T, PayPal, LC |
Delivery Way | Express (DHL, FedEx, UPS, TNT, EMS), By Sea, By Air, or as per your requirement |
  Â
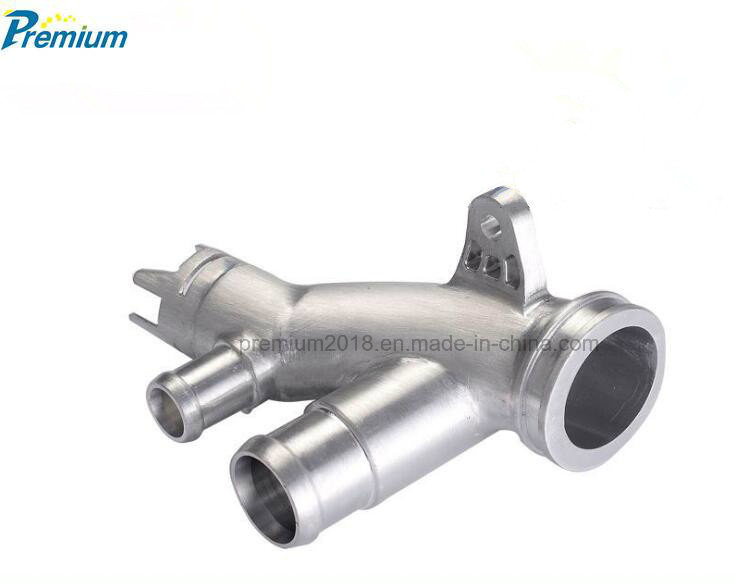
Send us your drawing, we can produce any design
Â
Â
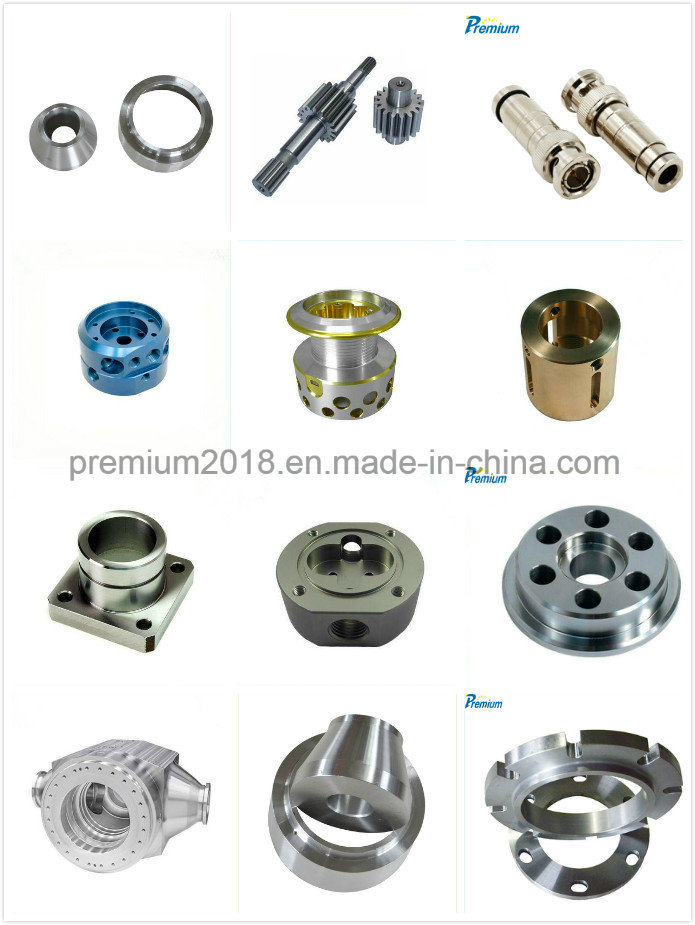
Company Information
Premium Rapid & Mold Industrial Co., Ltd.
Established in 2004, we are a professional manufacturer specializing in:
• CNC Machining
• Rapid Prototyping
• Mold Making
• Injection Molding
• Sheet Metal Stamping
We provide one-stop solutions from concept design, material selection, engineering, production, secondary processing, assembly, inspection, packaging, and shipping. Our products are used across various industries such as consumer electronics, home appliances, automotive, medical equipment, and more.
With over 14 years of experience in product development and operations management, Premium is known for cost-effective pricing, high-quality molds and parts, fast lead times, and excellent service. We have built strong customer trust through our reliable, accurate, and professional approach to every project.
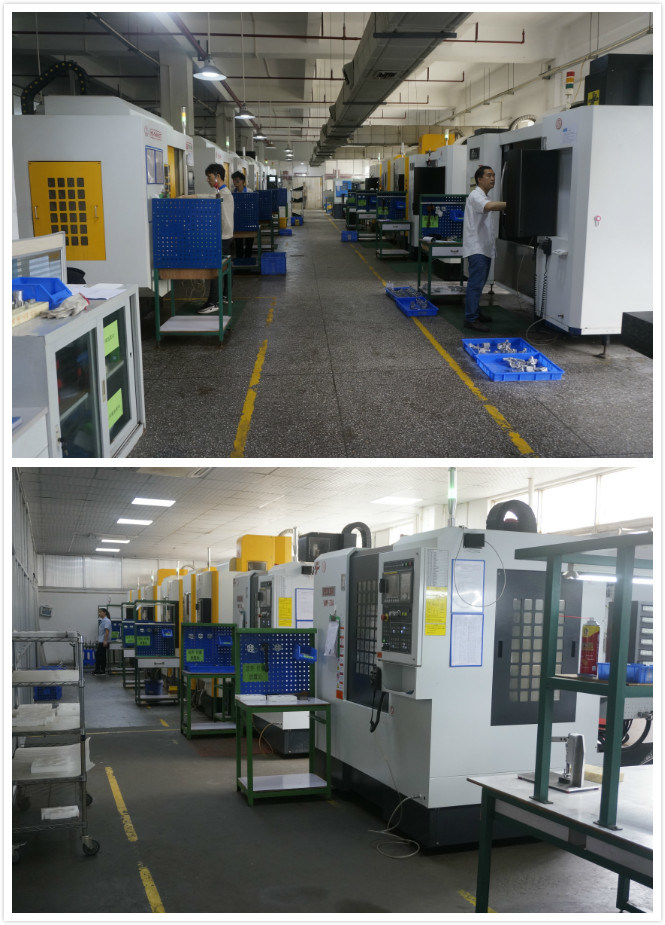
Our Services
Our Advantage
1. One-stop service
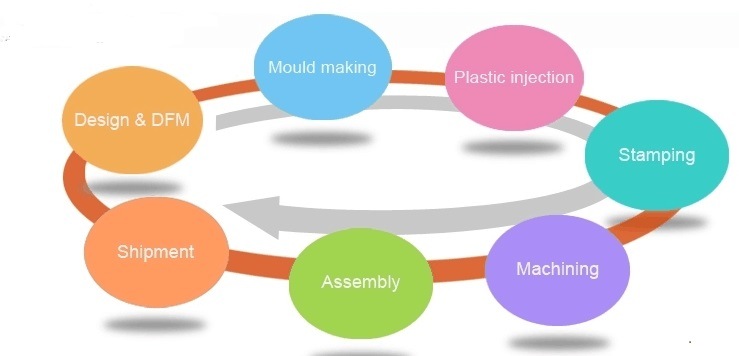
2. Tolerance: 0.005–0.1mm
3. Small orders accepted
4. Design assistance and full engineering support
5. High quality, low prices, fast turnaround
6. High-speed machining for shorter delivery and superior finish
7. Advanced equipment and skilled team
Continuously upgrading our technology to stay competitive.
8. Certifications: ISO 9001:2000
9. Skilled manufacturing for complex, thin-wall, and micro parts
10. Warranty: 100% quality guarantee or we will rework or refund.
Inspection Equipment
Quality is our culture!
For each order, we have a dedicated team to ensure quality throughout the entire production process, including:
FAIR (First Article Inspection)
DURPO (During Production Inspection)
PSI (Pre-shipment Inspection)
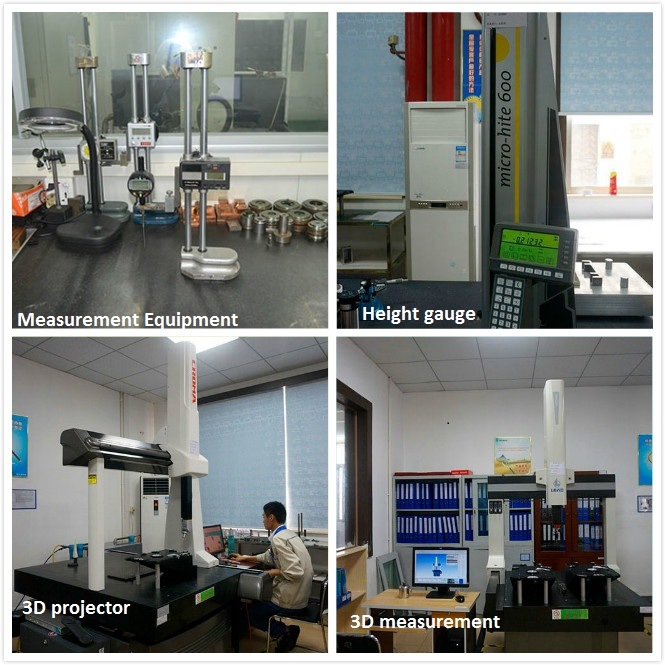
Packing & Shipping
Shipping: By sea, By air, By DHL, UPS, TNT & etc.
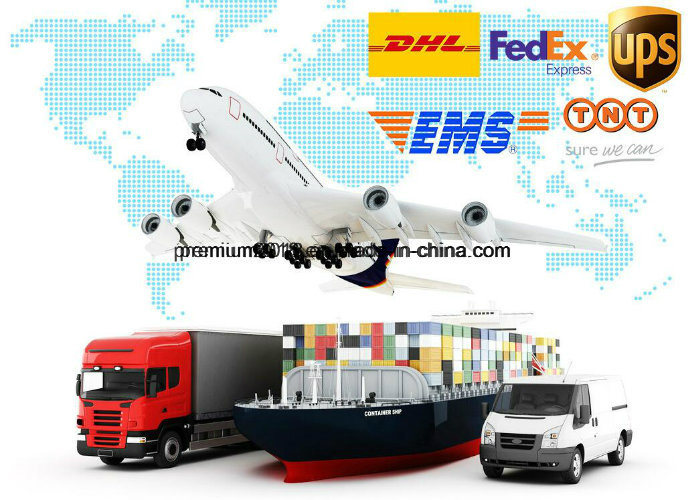
FAQ
1. Are you a factory?
--Yes, we are. We are a factory with a trading department.
2. What's the payment term?
--50% deposit, 50% balance via T/T before shipment if the order amount exceeds USD 2000.
3. What's the delivery time?
--Standard: 5–7 working days for samples. 12–30 working days for mass production.
--If you need urgent parts, we can prioritize and adjust the delivery time as needed.
4. What is the standard packaging?
--Separate blister plastic box or bubble wrap/pearl wool to prevent scratches and damage.
Contact Us
Amanda Zhou
Tel: +86-755-2729 8551
Mob: +86-18825428955
http://www.prm-mold.com
Your inquiry will receive a response within 12 hours.
If you have any questions or need more details about our products, feel free to contact us.
Induction brazing system is an advanced welding technology that uses high-frequency or medium frequency induction heating to heat the filler metal (brazing material) to a molten state and fill it into the joint between two or more workpieces. Through capillary action, the liquid brazing material wets the base material and solidifies to form a strong connection. This welding method has been widely used in many industries due to its fast, precise, and reliable characteristics.
working principle
The core of induction brazing system lies in induction heating technology, which generates an alternating magnetic field in the induction coil through alternating current. This magnetic field acts on the metal workpiece placed inside, causing eddy currents to be generated inside. The heat generated by eddy currents is sufficient to heat the brazing material above its melting point, but below the melting point of the base metal, thus achieving the goal of welding at a lower temperature.
component
Induction heating source: High frequency or medium frequency generator provides power.
Induction coil: used to generate a magnetic field.
Control system: Adjust heating power and frequency.
Clamping device: Fix the workpiece to ensure accurate positioning of the welding area.
Cooling system: prevents overheating, protects coils and workpieces.
Key advantages
High precision: It can precisely control the heating area and heating speed.
High productivity: rapid heating, significantly reducing welding cycle.
Strong adaptability: suitable for materials of different types and sizes.
Cost effectiveness: Low energy consumption and minimal material waste.
Environmentally friendly: Almost no smoke or harmful substance release.
Application scenarios
Induction brazing systems play an important role in the following industries:
Aerospace: engine blades, high-temperature alloy components.
Automobile manufacturing: transmission system, air conditioning system components.
Electronic engineering: connectors in microwave equipment.
Household appliance industry: Copper pipe connections for refrigeration equipment.
Jewelry: Welding of fine jewelry.
Development Trends
With the advancement of materials science and automation technology, induction brazing systems are developing towards greater efficiency and intelligence. For example, using artificial intelligence for process optimization, real-time monitoring and regulation of welding parameters, and improving the quality and consistency of finished products; Using nanotechnology and special coatings to improve the performance of brazing materials and broaden their applicability. In addition, the smaller and more portable design also makes the induction brazing system more competitive in mobile operations and on-site services.
Induction brazing machine, handheld brazing machine, high-frequency brazing machine, portable brazing machine,welding machine
Ningbo Dedao Electronic Technology Co., Ltd , https://www.nbdedao.com