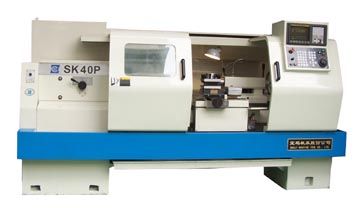
When evaluating a particular production component, one of the most important decisions a processing plant makes is whether to use a separate lathe and milling machine or to use a machine tool with multi-tasking capabilities for combined operations.
However, making this decision involves more than just making decisions about the adoption of multi-tasking machine tools. Some manufacturers tend to think of "multitasking" as a specific type of machine - a CNC lathe with a turret toolholder that can automatically change tools. Engineers at machine tool builder Mazak believe this is a mistake.
It can be said with certainty that a lathe capable of automatic tool change has high productivity. However, the design of this machine is also limited, and these limitations may be important to the workpiece. The design of other compound machine tools precisely overcomes these limitations. With all kinds of composite machining machines that have emerged today, it can be said that any potential "multi-tasking" workpieces may be produced with different levels of composite machine tools.
Michael Finn is a development engineer at Mazak, and Neil Drewsi is a software developer at the company. They are responsible for implementing and fine-tuning the composite machining application. They said that the most important step for a factory that has not implemented "multi-task" is to make up its mind. To perform composite processing properly, it may involve replacing CAM software, or even start using CAM for the first time. In addition, due to the way in which the composite machine tool holds workpieces, the machine's process may require that the tool configuration and tool path selection be different from those used on the machining center. A change to a multi-processing machine factory should be prepared for these changes. Once determined, increasing the machine to the optimum level requires only one more incremental factor.
Mr. Finn suggested that the following is the opinion of Mazak on the special “multi-tasking†equipment level:
Level 1 is a classic automatic tool changer. When turning a finishing part with this kind of machine, it can change the position of the workpiece to perform the drilling operation. Milling is also possible. Although there is no movement of the typical XYZ axis of a machining center, the machine can combine the X and Z axes with the rotation of the spindle or C axis. This actually means that all surfaces that are milled must follow the axis, radius, or contour of the workpiece.
Level 2 overcomes the limitations of machining by adding a Y-axis. With the Y-axis, drilling operations can be off-center, not just machining radial or axial holes. This freedom of movement also allows milling with eccentric, tight tolerances. Precision keyways are examples of this milling feature, and it is much easier to implement it on this level of machine.
Level 3 is the introduction of a milling spindle that makes it almost comparable to a machining center. At this level, the machine began to change its similarity with the lathe. This machine tool does not provide rotation driving force by the tool holder, but uses a milling spindle to lock its rotation and clamp the stationary tool for turning. If level 1 and level 2 machines can be referred to as "turn-mill" beds, then level 3 machines can be described as "milling car" beds.
This is a major change. There are several advantages to replacing a toolholder with a spindle. One is milling power. The large spindle power allows the machine to use heavier milling passes than on the automatic tool changer. Another advantage is the adjustment of the angle function, thanks to the "spindle indexable" method for B-axis positioning. This allows milling and drilling at an angle that is independent of the axis of rotation of the workpiece.
The last advantage is the ability of the machine tool to use the tool. Although the space for holding the tool is a limiting factor for the tool holder, the Class 3 machine can avoid this limitation by integrating the tool changer and the tool magazine like a machining center. Mr. Finn said that some factories choose this type of machine tool not because of the special geometry of the workpiece, but because of the adjustment and saving. The various tools in the machine tool magazine are in place, and the use of a knife is very simple.
Lemon Squeezer
PREMIUM QUALITY - Commercial grade, Best Quality Jumbo size press, made from the STRONGEST highest quality 18/10 STAINLESS steel with hand polished finish that will not peel or rust. Dish Washer Safe and easy to clean.
DURABILITY : 100% Dishwasher Safe, Will never break, Will never rust - Guaranteed !
EASY TO USE : Simply cut fruit in half, and place it cut-side down in the bottom bowl of squeezer, and squeeze the handle. You will be able to squeeze maximum juice out of fruit in a way that you never imagined possible.
Lemon Presser,Orange Squeezer,Aluminum Lemon Squeezer,Stainless Steel Lemon Squeezer
YANGJIANG TOALLWIN TRADING CO., LTD , https://www.kitchenknife.de