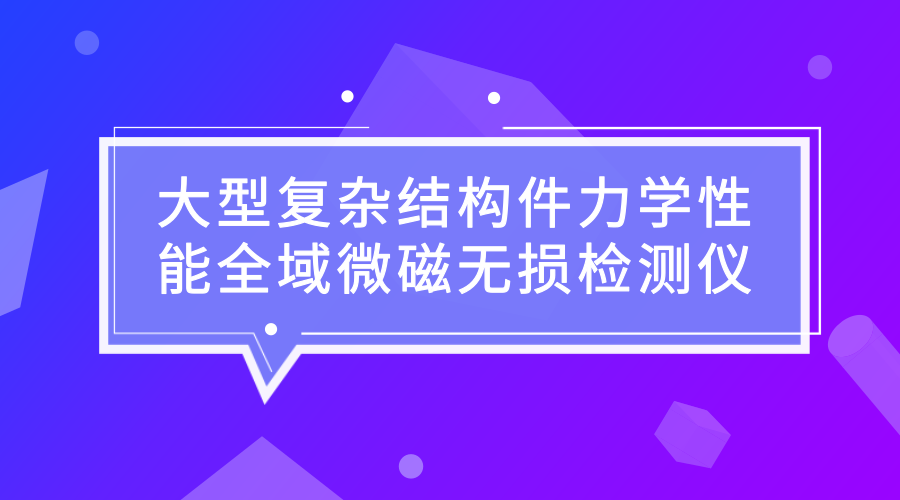
The QNP Steam Turbines` capacity mainly covers 200MW and below, include NI series (Normal Impulse Turbines) and HE series (High Efficiency Turbines). Our steam turbines are flexible and diverse in structure and layout so as to meet various requirement of our users. Aiming at the global leading equipment manufacturing enterprise, our design and R&D standards are higher than GB standard and in the same league with European and American energy equipment manufacturers.
1.Characteristics of QNP Turbine
- High speed, high efficiency, low energy consumption
- Highly integrated three platform and one station, require smaller space
- In-the-factory assembly and whole machine transportation make site installation easier, faster and more economical.
- Single-tier and direct exhaust, condenser floor installation, lower construction cost
-
QNP adopts advanced small pitch-circle technology in its high-end high efficiency turbine products, and hence considerably improved the turbines`flow efficiency.
-
By combining the advanced technology of European turbine with QNP technology, and optimizing the integration between imported advanced R&D tools and advanced domestic design software, QNP has solved the universal defect of inter-stage efficiency loss in most domestic units.
-
Using 3D bending-torsion blade design to improve the final and penultimate stage efficiency and structural strength to ensure long-time continuous operation of the unit.
-
Using high-speed running design and full-cycle steam distribution to improve the unit`s flow efficiency, reduce space occupancy, and make the installation more efficient.
-
Optimized enthalpy drop distribution design, through the comparison of tens of thousands of design data, form the best single-stage enthalpy drop distribution solution to ensure that each unit is in its maximum efficiency.
-
High-precision and high-quality manufacturing process: to ensure the high precision and high quality of key dynamic and static components, the flow passage components are processed by four-axis or five-axis CNC machining center.
-
Specially produced for high-end users, each component is carefully designed and the unit always presented to the customer as a flawless modern industrial artwork.
-
Maximum internal efficiency may reach 88%
2.Technical characteristics of parts
Gland sealing matching: the industry-leading and advanced gland sealing structure design reduces the steam leakage loss.
Blade assembling: the optimized blade molded lines are designed by the international advanced design software and processed by high-grade, high-precision and advanced technology which improve the thermal efficiency greatly.
Governing system: advanced governing methods are used for high control precision and fast response speed and which also has the electronic over-speed trip function, load shedding trip function, as well as auto start, grid connection and on-load function.
Rotor: we have shrink-on rotor and solid forging structure rotor which are all processed by Mitsubishi Planer machine and adjusted by vacuum high speed dynamic balancing machine to make sure the vibration of each position of bearing is in good state when the Steam Turbine running. Small vibration of the rotor we produced is a distinctive characteristic of our products.
Condenser: the stainless steel screwed pipe is used as heat exchanger with good anti- pollution ability and high heat-exchange efficiency. High-quality titanium tube is used when the cooling water is seawater. We use digital controlled lathe for drilling hole.
Casing: the split is processed by one-off molding technology and the precision of which can be 0.0058MM without any steam leakage. The concentric circles of the whole axis are processed by high precision turn-milling of the 5-joint axis machining center.
Diaphragm: we use qualitative carbon steel as the support and make the flow field better comply with the design via special welding technology so as to improve the internal efficiency.
Lubricating oil system: the multiple filtration technology--impurity strainer of oil tank, double bucket strainer for refined filtration, bearing inlet strainer which can be replaced during running--make the turbine oil entering the bearing bush achieve the best performance.
Control and protection system: QNP uses the Siemens microprocessor as the core of the system to ensure the stability and timeliness of signal processing. For important signal, multistage redundancy functions are introduced to ensure the safe and stable operation of equipment. Friendly interface makes operator work easily. More than 3-monthes` record of operating data can be saved by recording system and also can be extracted at any time.
3.Various layout and application
Except the general double-tier layout structure, we also developed steam turbine with single-tier and fast-installation layout structure, mainly includes:
(1)Oil tank as base plate:
The position of oil tank for Condensing Steam Turbine can be designed under the steam turbine as the base plate with the steam turbine, bearing pedestal and gear box on it which has same horizontal plane with condenser.
(2)Three platform and one station steam turbine:
Composed of steam turbine base plate, auxiliaries base plate, control base plate and centralized oil station for a convenient installation and layout at site. And the centralized pipeline will let the site more clean and tidy.
(3)Axial exhaust type
Mainly applied in 15-50MW condensing and pumping condensing high efficiency turbine. This type of steam turbine adopted single-tier arrangement, with axial exhaust directly into the condenser. Suitable for whole machine delivery, and can considerably shorten the installation period and reduce civil engineering costs.
Steam Turbines
Steam Turbines,Steam Turbine,Back Pressure Steam Turbine,High Speed Steam Turbine,High Efficiency Steam Turbine,Extraction Condensing Steam Turbine
Shandong Qingneng Power Co., Ltd. , http://www.steamturbine.be