
Precision Plastic Injection Mold for Car Automotive Light and Sensor Parts
Mold Description | Â |
Mold Standard | DME or HASCO |
Mold Base | LKM, DME, HASCO, FUTABA |
Cavity/Core Steel | H13, S-7, S136, SS420, NAK80, P20, and other materials as per requirement |
Hot Runner | Yudo |
Cavity | Multi-cavity or single-cavity |
Gate Type | Side gate, Sub-gate, Pin-point gate, Edge gate, etc. |
Hydraulic Cylinder | PARKER, TAIYO, STAUBU, JUFAN |
Mold Components | DME, Progressive, PCS, Punch, Royal, etc. |
Steel Treatment | Heat treatment, Nitriding, Chrome plating |
Surface Finish | SPI standard, VDI EDM, Texturing, etc. |
Texturing | Mold-Tech, Yick Sang, Ni Hong, Tanazawa, etc. |
Plastic Material | PP, PC, ABS, PE, HDPE, PET, POM, PMMA, PA (GF), PBT (GF), PVC, PPS, etc. |
Product Weight | 5.0g – 15kg |
Mold Life | 0.3 million – 1 million shots |
Delivery Time | 4 weeks for T1 samples, exact time depends on mold complexity |
Packaging | Free-fumigation three-plywood case for molds, cartons for parts |
Design Software | CAD, UG, Pro/E, SolidWorks |
Value-Added Services | Dust-free spraying, silk-screen printing, ultrasonic welding, thermal bonding, assembly, prototyping |
Service Area | Transparent, overmolding, two-color, air-assisted forming, deep barrel, design R&D, assembly |
Our Capabilities | Auto, Aerospace, Household, Electrical, Industrial, Medical, Toys, Office, Cosmetics, Outdoor, OA Equipment, etc. |
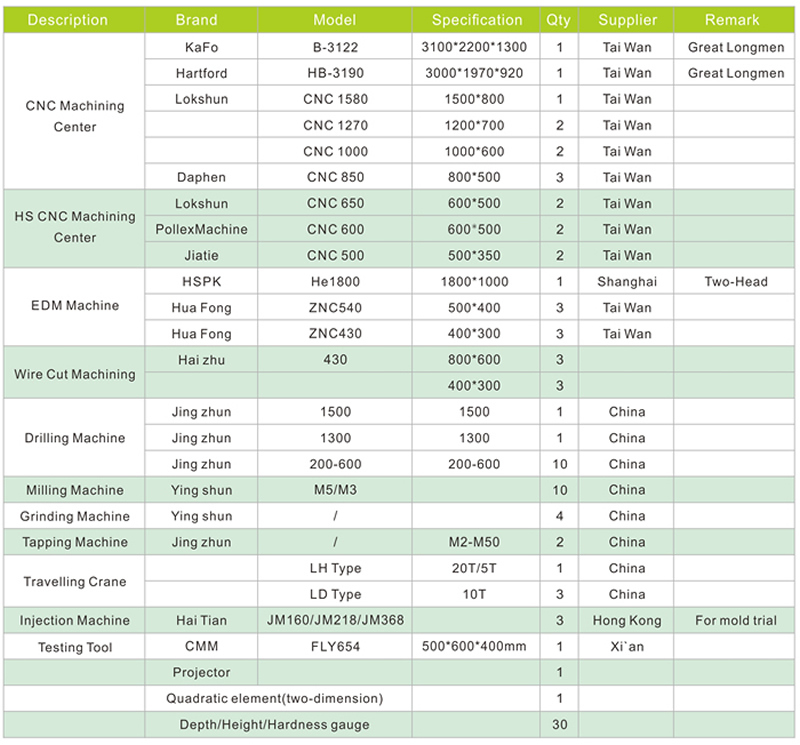
Sample Show
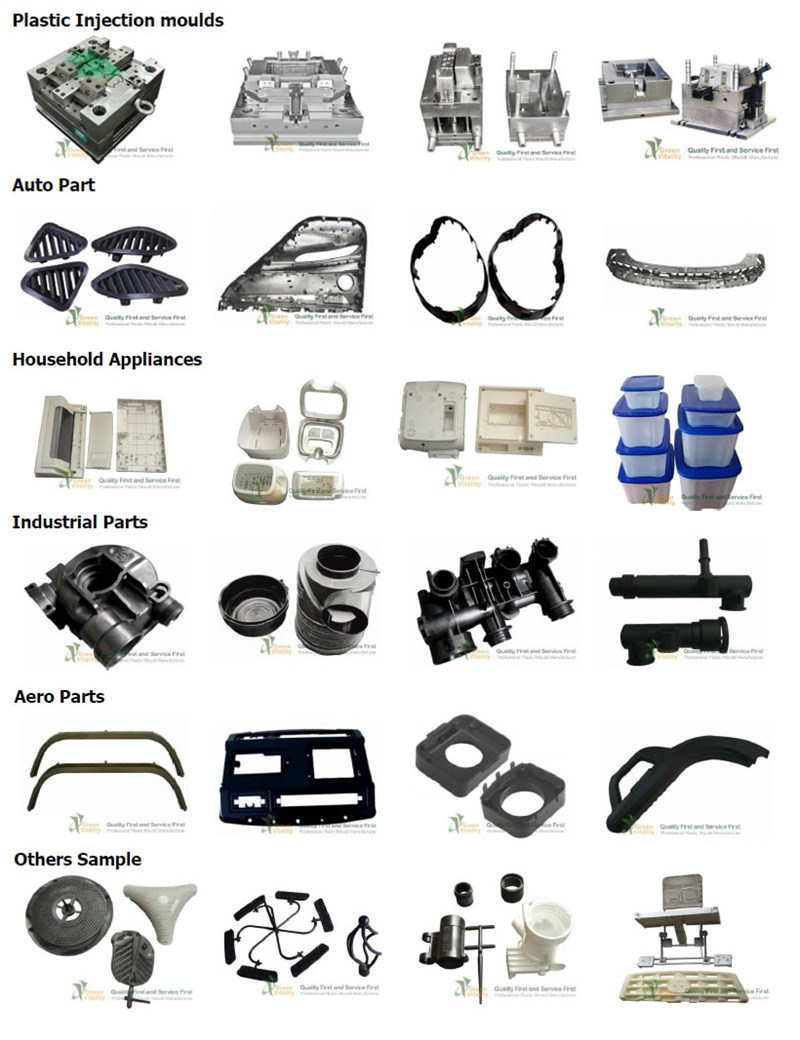
Production Process
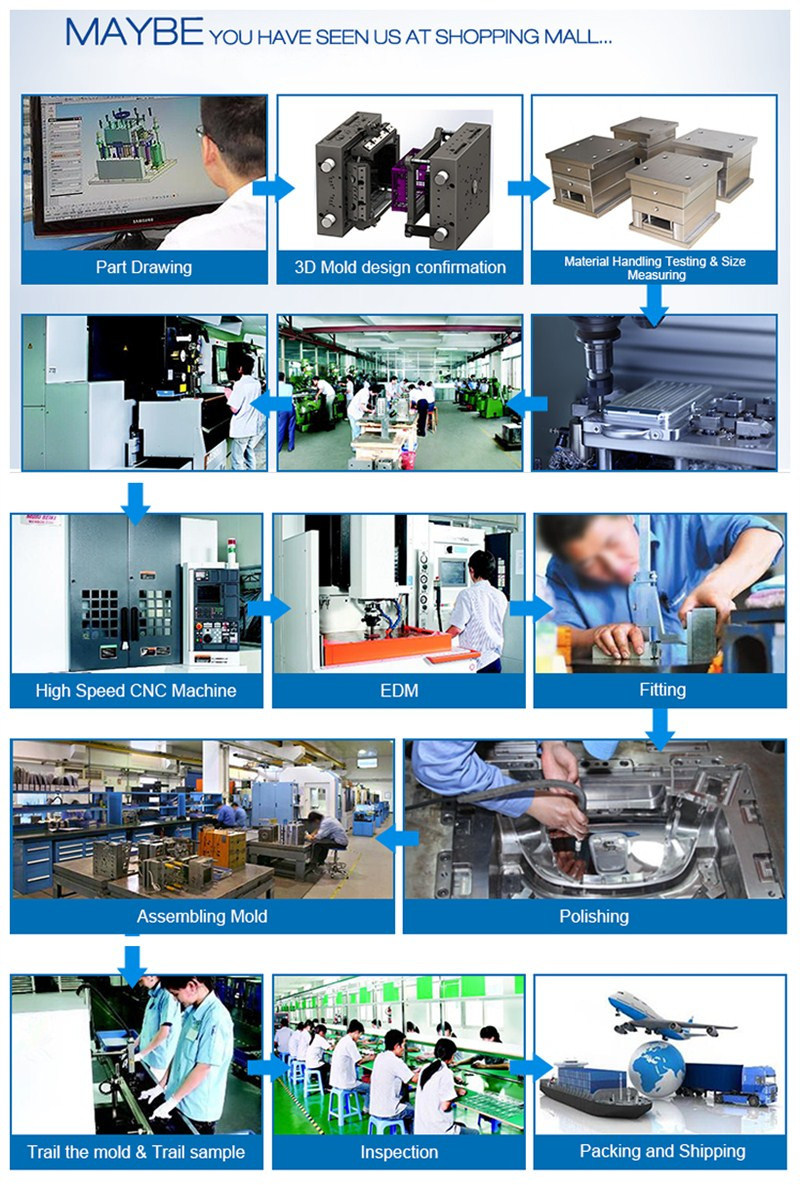
Company Profile
Green Vitality was established in 1993, starting from a small CNC machining workshop in Chang'an town. With over 25 years of experience in custom tooling and injection molding, we have grown into one of the leading global mold manufacturers, specializing in large plastic injection molds. Our company follows a modern business management system and adheres to ISO 9001:2015 quality guidelines. We are equipped with advanced manufacturing equipment, skilled engineers, and a dedicated team, ensuring that we deliver high-quality molds and plastic parts. We serve a wide range of industries, including automotive, aerospace, household appliances, industrial, and medical sectors.
We produce more than 400 molds annually, with most of our products exported to countries like the USA, Germany, France, Turkey, and Italy. We maintain long-term partnerships with our clients by consistently delivering top-quality molds and parts, aiming to build strong strategic relationships that ensure mutual success and growth.
Factory Profile:
6,000 square meters of mold-making workshop, 8,000 square meters of injection molding workshop.
160 employees, including 20 engineers, 65 mold makers, and 60 injection molding operators.
Factory Capacity:
Up to 40 molds per month
Maximum mold size: 3200x2200mm
Maximum mold weight: 25 tons
Service Scope:
Specializing in large plastic molds for automotive, aerospace, and household appliance industries
Plastic injection molding
Prototype development
Market Advantages:
High-quality molds and plastic parts
Reliable and timely service
Â
Commercial Pull Down,Commercial Pull Down Trainer,Commercial Pull Up Trainer,Commercial Pull Up Trainer
HEBEI HONGKANG SPORTS EQUIPMENT CO., LTD , https://www.hkangsports.com