[ Instrument Network Instrument R & D ] Recently, Liu Wei and Yang Bing, associate researchers of the Electron Microscopy Technology Research Group of the Energy Research Technology Platform of the Dalian Institute of Chemical Physics, Chinese Academy of Sciences, teamed up with a team of researchers from the Shanghai Institutes of Advanced Technology, Chinese Academy of Sciences, and Gu Meng, an associate professor at Southern University of Science and Technology Progress has been made in observing and confirming the true surface of NiAu catalysts in CO2 hydrogenation reactions.
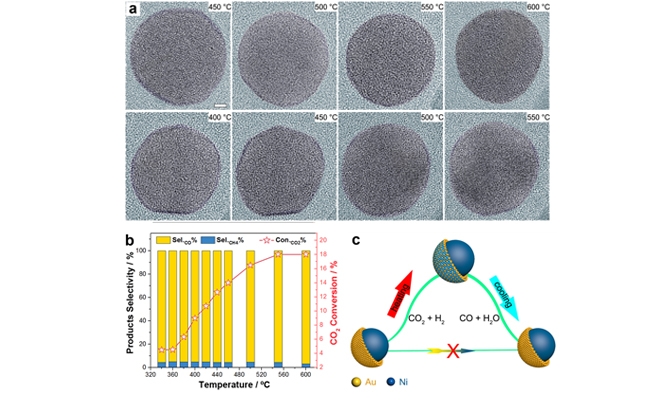
In catalytic research, conventional static microscopic analysis can only provide non-operating structure information of the catalyst before or after the reaction. However, under the effects of thermal vibration and gas molecule adsorption / desorption, the surface atoms of the catalyst will inevitably migrate and cause surface reconstruction. The changed surface is the real surface related to the catalytic reaction activity. To see this surface state requires With in situ characterization technology. Especially for polymetallic catalytic systems that are prone to surface restructuring, the atomic structure of the catalyst in the reaction atmosphere cannot be observed in situ, the real surface contributing catalytic activity cannot be confirmed, and a reliable catalytic structure-activity relationship cannot be established. In previous studies, in-situ spectroscopy with macro-statistical properties has pioneered exploration of dynamic catalytic processes from the fine energy dimension, such as in-situ FTIR, in-situ XPS (AP-XPS) and in-situ XAS . Based on this, direct observation of the surface atomic arrangement of the catalyst in the reaction in real space is a long-term goal pursued by researchers. In response to this problem, Environmental Transmission Electron Microscopy (ETEM) was born. ETEM is an in situ method mainly based on TEM imaging, which is suitable for tracking the structural evolution of catalysts in gas-solid phase reactions under atomic resolution.
In this work, the research team studied the process of CO2 hydrogenation catalyzed by the NiAu / SiO2 system based on environmental transmission electron microscopy and a specially designed mbar-level negative pressure quantitative air-mixing system. The initial static microscopy results show that the catalyst has Ni as the core, and the surface is coated with 2 to 3 Au atom shells, which is a typical Ni @ Au core-shell configuration. Considering that Ni has strong hydrogenation activity, it will lead to the CH4 selectivity of the reaction. Therefore, this core-shell configuration can reasonably explain the CO selectivity of CO2 hydrogenation of more than 95% in this work. However, in-situ observation of environmental transmission electron microscopy found that under the reaction atmosphere and temperature, the core Ni atoms of the catalyst will gradually segregate to the surface and alloy with Au; when the reaction is cooled down, it will be unalloyed and returned to the Ni @ Au core-shell structure . The results of in situ spectroscopy (including in situ FTIR and in situ XAS) confirm the above microscopic observations well. Theoretical calculations and in-situ FTIR results show that the in-situ CO and NiAu surface alloying play a key and subtle role in the reaction, which is the reason for the evolution of the catalyst configuration and the high CO selectivity. This work provides inspiration for the study of core-shell bimetal catalytic processes. For example, does the core-shell surface actually exist under reaction conditions, and does it contribute catalytic activity? For example, is it necessary to pursue the construction of core-shell surfaces in catalyst preparation?
This work is a set of comprehensive application cases of microstructure characterization and macrostatistics statistics in the in situ environment. At the same time as highlighting the microscopic observation of the local atomic structure, the in situ spectroscopy method, especially the in situ XAS technology, ensures the electronic display. Confidence in correlation between micro-discovery and material performance under macro conditions. It provides an example for the development of new methods and technologies for in situ, dynamic, and high space-time-resolved catalytic characterization, and also provides reference and thinking for the design and construction of new materials with specific structures and functional catalysis.
Advantages of Casting Process:
1: Suitable for complicated structures.
2: Customized, made to customer's drawing or prototype.
3: Casting provides Precise shape, less material machining.
4: Wide weight variation allowed,from 1kg to 40kgs.
5: Wide range of material spec can be selected:
GG450,GG500,GG700,ASTM 65-45-12, SIMO Alloy Iron
6: Parts can be used for different industries, Auto Exhaust Pipe, Hydraulic, Agricultural Machinery Parts
7: High temperature resistant
Certificastes and Documents Provided:
- PPAP
- CPK
- SPC
- MAS
- Non-Destructive Report, UT,MPT
Packaging and Transport : Plywood Case packing
1) Standard plywood case for outside packing.
2) Rusty proof oil or liquid applied for each part.
3) Parts are segerated one by one with plastic plate.
Delivery Terms:
- FOB
- DDU
- DDA
- CIF
- CNF
Our Services
1: MOQ: 5 pcs
2: Sampling Time: 30 days including moulding
3: Within 24 hours response for each email
4: Flexible payment terms provided
5: Weekly project update
Exhausting Pipe Components
Exhaust Pipe Part,Exhausting Pipe Components,Car Exhaust Pipe Component,Car Exhausting Pipe Component
J.B MACHINERY (NINGBO) CO., LTD. , https://www.jbcastings.com