In the deep hole processing, the deep-hole drilling chip in the wrong tooth has been widely used due to its good chip separation effect, smooth chip removal, high processing efficiency, and high processing precision. However, there are still some deficiencies in the common swarf deep-hole drilling swarf. Aiming at these problems, we have designed a new type of deep-hole drill with internal swarf in the wrong tooth. Through practical use and cutting performance tests, we have proved that Hole drill has good cutting performance and application effect. The problems of ordinary deep-hole drilling with internal swarf removal are common. The internal deep-hole drilling with internal swarf, according to the size of the drill bit, can be divided into 3 teeth or 5 teeth. Each tooth is external and internal. And middle teeth, because the middle tooth and the center tooth and the outer tooth are not on the same cone surface, but have a H value (axial direction) higher than their cone surface, so it can obtain a better chip separation effect, and each blade tooth Different blade materials can also be selected according to their different cutting conditions. However, there are also some deficiencies in the structure and geometric parameters of the cutter teeth in the common wrong-tooth swarf deep-hole drill. The main manifestations are as follows: The front angle 2F is smaller, the drill tip is higher, and the lag between the outer teeth and the guide block is larger. Large, long time for entering and drilling can easily result in broken teeth and chipping in the drilling process. The durability of the drill is low and the drilling quality is also poor. Because the front angle is smaller, each blade tooth is arranged along the radius on the drill cone surface in sequence, and the axial height difference between the teeth is relatively large. Therefore, in the drilling and drilling stages, the central teeth must bear large axial and radial forces independently, which results in large cutting vibrations, poor centering effect, and easy chipping. The corner angles of the middle and outer teeth are smaller, the sharp corners protrude, and the strength is reduced. Once the sharp corners are worn, the amount of lap joints between the teeth is destroyed, and it is easy to cause a tooth abutment and a twist drill accident. The inner edge declination angle t2 is smaller, the height of the anti-cone at the bottom of the hole is lower during drilling, the centering effect is weakened, and the cutting vibration is easily caused. During the drilling process, the combined radial force acting on the drill should always point between the two guide blocks to ensure that the drill is in a stable cutting state. However, due to the limitations of the drill diameter and the blade size, sometimes the designed drill bit has a smaller radial force, and when the blade wears or meets a hard material point, the radial resultant force will point in the opposite direction instantaneously. It will lose the drilling balance and cause vibration, which will cause drilling deflection and spiral groove problems, affecting the drilling quality. Structure and edge characteristics of a new type of deep-hole drill with internal swarf removal

Fig. 1 New type of fault-tooth internal chip removal deep hole drilling For common problems of common deep-hole drilling chip internal drilling, we use the deep-hole drilling chip in the common wrong teeth to perform correspondingly on the bit structure and blade shape. Improvements have been made in designing a new type of deep-hole drill with internal swarf removal (also known as multi-tipped internal swarf deep-hole drill). Its head structure and blade shape are shown in Fig. 1. Its structure and cutting edge are The main features are as follows: The bit sharpening angle is increased to further reduce the axial height difference between the cutter teeth, shorten the time for entering and drilling, and reduce the unstable drilling time to improve the durability of the bit. The center tooth on the right side of the axis is ground into a tine, so that the bottom of the processed hole forms a centering ring groove, and the inner edge angle t2 is increased so that the bottom of the hole is formed with a higher centering resistance during drilling. Cone (see Figure 2), double centering and stable drilling. With the exception of sharp corners on one side of the teeth and the outer edge, all the other teeth are chamfered, with a side back angle of 6° to 12°, eliminating sharp corners and increasing the heat dissipation volume of the teeth. The strength of the cutting teeth is enhanced, and it is not easy to collapse the blades, which helps to improve the durability of the drill.

Figure 2 The shape of the bottom of the machined hole
Increase the eccentricity of the drill tip e, and grind the two inner edges of the center line on the inner edge of the center tooth, that is, the inner edge is composed of different line angles with different inclinations. This effectively reduces the drill height Dh. The time for entering and drilling is shortened, so that the stable drilling phase can be quickly entered during drilling, and the center tooth and the middle tooth cut into the workpiece almost simultaneously, which can improve the stress state of the cutting teeth and reduce the cutting vibration. When drilling, because the drilling time is short and the cutting cap is thin, the cutting force on each tooth disappears at the same time, which is beneficial to damping and improving drilling stability. According to different cutting loads and cutting conditions of the cutter teeth, the center teeth are subjected to a large axial force, and the extrusion and friction are severe and the cutting conditions are severe. The YG-type inserts with high bending strength and good impact resistance can be selected. Because the cutting speed of the outer teeth and the middle teeth is higher than that of the center teeth, the blade materials with good red hardness and high wear resistance should be selected, such as YT798 and YW1. A damping block is added at the rear end of the cutter body to protect the cutter teeth and improve the shape accuracy of the machining hole. When the cutter tooth wears or the chipping causes the drilling vibration, it can play the role of vibration reduction and vibration elimination. Reduce the height between the guide block and the body and increase the flexural strength of the guide block. At the same time, in order to increase the cooling liquid area, a rectangular or semi-circular trough is milled on the cutter body so that the flow area can be increased by 20%~30%, and the coolant flow can be increased to enhance the drilling process. Cooling lubrication effect. Cutting Performance Test of New Type of Wrong Internal Debris Deep-hole Drill In order to verify the cutting performance of the new type of internal tooth removal deep-hole drilling, firstly, the cutting force comparison test with ordinary type deep-hole drilling of the wrong tooth was performed to analyze two kinds of drill bits. The size of the cutting force and the smoothness of the cutting; followed by the drilling test of the batch part to test the durability, processing quality, and processing efficiency of the new drill. Contrast tests of the cutting forces of the two types of bits were performed using a C630 lathe modified deep hole drilling boring machine. The workpiece material was 40Cr alloy steel, hardness HRC28~32, and the drill diameter was F58.4mm. The method of measuring the axial force and the change of the torque during the cutting process is performed by attaching a resistance strain gauge on the drill pipe and connecting a measuring instrument. From the drilling test data, the axial force and torque of the two types of drill bits increase correspondingly with the increase of the feed amount f, but the new deep hole drills have an average axial force reduction of 21% compared with ordinary deep hole drills. The average decrease was 14.7%. Moreover, as the feed rate increases, the cutting force of the new deep hole drill increases more slowly. For example, when f = 0.03 mm/r, the axial force of the new type of deep hole drill is only 25% lower than that of the ordinary deep hole drill. The torque is reduced by 24%; when f = 0.25mm/r, the axial force and torque are reduced by 20.7% and 22.7%, respectively. It can be seen that the new deep hole drills are lighter and more stable in the cutting process with large feed rates. In addition, from the recorded momentary changes in the axial force can also be seen at a large feed rate (f = 0.25mm / r), the new deep-hole drilling force fluctuation peak, trough value is only equivalent to ordinary One-third of the deep-hole drills indicate that the new deep-hole drilling is stable. This is consistent with the fact that the centering annular groove and the centering reverse cone can be used for double centering and stabilizing drilling effects when drilling with a new deep hole drill. Drilling vibration, durability and processing quality of the comparative test of these two kinds of drill bits for bulk drilling machining test, choose to perform actual processing in a petroleum machinery plant, machine tools for the T2130 deep hole drilling boring machine, workpiece material 40CrNiMo5 alloy steel , hardness HB250 ~ 300, drilling diameter = 50.4mm.

Figure 3 Drill pipe amplitude comparison curve
A dial indicator is installed at the drill rod at the rear end of the oil distributor to measure the vibration of the drill bit during the cutting process. When the center tooth (point A), the guide block (point B) and the damping block (point C) enter the drill The amplitude of the drill pipe and the comparison curve of the drill pipe amplitude between D and E are shown in Figure 3. It can be seen that the vibration of the new deep hole drill during the drilling and the entire drilling process is smaller than that of the ordinary deep hole drill. And after point C, the new deep hole drill has a vibration stabilization process after its damping block enters the workpiece, so that the drilling torque is rapidly reduced to normal level, while the ordinary deep hole drill does not have this process. At the time of drilling (between D and E), the vibration of the common deep hole drill began to increase and the amplitude increased. The new deep hole drill, due to the small height difference between the teeth, was drilled almost at the same time, and there was protection for the damping block. The effect can be smoothly drilled and the amplitude increase is small. After two kinds of drill bits are used for drilling the bulk parts, when the flank with the same size is worn out, the average length of the drill holes in the new false teeth can be up to 16m, which is the length of common deep-hole drilling holes More than 2 times. The quality of boreholes is measured. The boreholes drilled by the new deep hole drills are approximately 3 μm smaller than the ordinary deep boreholes, and the aperture enlargement is smaller by 0.04 mm. The bore size accuracy can reach IT7~IT8, and the surface roughness Ra. = 1.0 to 3.2 μm. Concluding remarks The structure and edge shape of the new false teeth internal chip removal deep hole drill are proved to be reasonable by the cutting performance test, which can effectively improve the stability of drilling, prolong the service life of the drill bit, and improve the precision of hole machining. It is a good application effect. A new type of faulty internal chip deep hole drill bit.
Professional Food Printer for cakes,biscuit,chocolates
1.The Chocolates Printer is used to print pictures on food.
2.It has 6 colors which can print colorful and bright pictures.
3.The print effect is vivid.
4.The machine can replace the Manual labor.
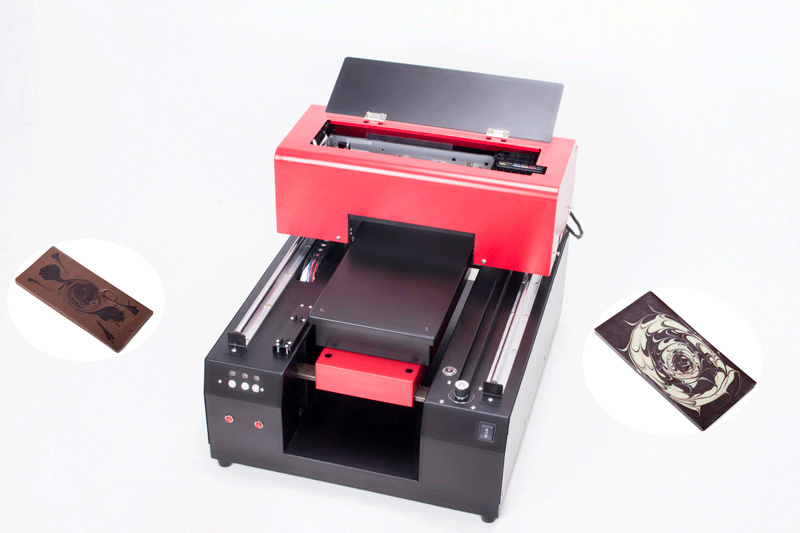
Name
|
Chocolates printer
|
Print head
|
DX5
|
Print size
|
21*38cm
|
Print color
|
CMYK+LC LM
|
Print speed
|
A4 photo/163s
|
Printing resolution
|
5760*1440dpi
|
Nozzles
|
90*6=540
|
Interface
|
USB 2.0
|
Net weight/Gross weight
|
35kg/42kg
|
Printer size
|
57*48*44cm
|
Height adjustment
|
Handle/Automatic
|
Working power
|
110-220 50-60Hz 30W
|
Operation system
|
Windows 2000/XP/WIN7/Vista etc.
|
Temperature
|
5-35º
|
Chocolates Printer
Chocolates Printer,Food Chocolate Printer,3D Chocolates Printer,Digital Chocolates Printer
Shenzhen Refinecolor Technology Co., LTD. , https://www.szcoffeeprinter.com