1, casting technology (1) smelting
For the melting of high-grade cast iron, a large-capacity intermediate frequency furnace will be used for smelting or variable-frequency intermediate frequency furnace smelting, and a direct reading spectrometer will be used to detect the molten iron composition. Ductile iron treatment adopts subcontracting to develop a new variety of spheroidizing agent, and adopts advanced gestation methods such as gestation, intra-type gestation and compound gestation. The parameters of the melting process enable microcomputer control and screen display.
(2) Modeling
Lost foam casting will be developed and promoted. In sand casting, boxless injection molding and extrusion molding will be valued and will continue to be promoted in new or rebuilt plants. The original high-pressure molding line will continue to be used, and some of the key components will be improved to achieve automatic core and lower core.
2, forging technology
The automatic line with hot forging press and electro-hydraulic hammer as the main engine is the development direction of forged crankshaft production. These production lines will generally adopt precision shearing, roll forging (cross wedge rolling), medium frequency induction heating, finishing hydraulic press. Advanced technology such as precision pressing, and equipped with a robot, conveyor belt, and a die changer with a rotary table to form a flexible manufacturing system (FMS). FMS automatically replaces workpieces and molds and automatically adjusts parameters for continuous measurement during operation. Display and record data such as forging thickness and maximum pressure and compare with the set value to select the best deformation to obtain a quality product. The entire system is monitored by the central control room for unmanned operation.
3. Mechanical processing technology
Crankshaft roughing will use CNC lathes, CNC internal milling machines, CNC broaching machines and other advanced equipment to perform CNC turning, internal milling and car-broaching on the main journal and connecting rod journals to effectively reduce the deformation of crankshaft machining. Crankshaft finishing will extensively use a CNC-controlled crankshaft grinder to finish the journal. The grinding machine will be equipped with the automatic dynamic balancing device of the grinding wheel, automatic tracking device of the center frame, automatic measurement, automatic compensation device, automatic dressing of the grinding wheel, constant line speed and other functional requirements to ensure the stability of the grinding quality. High-precision equipment relies on the status quo of imports and is not expected to change in the short term.
4. Heat treatment technology and surface strengthening technology
(1) Crankshaft medium frequency induction hardening
The medium frequency induction hardening of the crankshaft will adopt the microcomputer monitoring closed-loop medium frequency induction heating device, which has the characteristics of high efficiency, stable quality and controllable operation.
(2) Crankshaft soft nitriding
For high-volume production of crankshafts, in order to improve product quality, a microcomputer-controlled nitrogen-based atmosphere gas soft nitriding line will be used in the future. The nitrogen-based atmosphere gas soft nitriding production line consists of a front washing machine (cleaning and drying), a preheating furnace, a soft nitriding furnace, a cooling oil tank, a post-cleaning machine (cleaning and drying), a control system, and a gas-making gas distribution system.
(3) Crankshaft surface strengthening technology
Ductile iron crankshaft fillet rolling strengthening will be widely used in crankshaft machining. In addition, the composite strengthening process such as round roll rolling strengthening and journal surface quenching will also be applied to crankshaft machining. Forging steel crankshaft reinforcement will be more The ground is treated with a journal and rounded corners.
Introduction:
Magnetic Lifters have strong magnetic path made by strong NdFeB magnetic material which supply permanent power. Our permanent magnetic lifters are made use of in a variety of industries. Our permanent magnetic lifters can hoist iron, steel blocks, cylinder and others and provide a quick and convenient method of loading, unloading, and moving. Our permanent magnetic lifters are the most ideal lifting equipment for factories, warehouses, docks and transportation.
Manual Magnetic Lifter Features:
• Use to lift and transport steel and iron for factories, docks, warehouses, transportation and more.
• Turning the manual handle activates or turns off the magnet.
• Strong attraction gives this tool a powerful lifting ability while it`s small size and light weight makes it easy and safe to operate. Effective for long periods with no need for a power supply.
• The safe coefficient of magnet lifter is 3.5.
Specifications:
Type |
Rated Load/kg |
Max Breakaway |
Size(mm) |
Net Weight(kg) |
|||
L |
B |
H |
R |
||||
PML-100 |
100 |
300 |
123 |
62 |
67 |
140 |
3 |
PML-400 |
400 |
1200 |
195 |
95 |
92 |
160 |
9 |
PML-600 |
600 |
1800 |
246 |
120 |
115 |
220 |
20 |
PML-1000 |
1000 |
3000 |
298 |
153 |
135 |
250 |
36 |
PML-2000 |
2000 |
5000 |
395 |
172 |
165 |
350 |
68 |
PML-3000 |
3000 |
7500 |
480 |
175 |
165 |
350 |
80 |
PML-4000 |
4000 |
10500 |
560 |
175 |
165 |
360 |
109 |
PML-5000 |
5000 |
12500 |
570 |
230 |
215 |
680 |
192 |
PML-6000 |
6000 |
15000 |
780 |
230 |
215 |
720 |
218 |
Features:
Zero electricity required
Forged hook for high mechanical strength and durability
Precision machined assembly block in single piece to enhance efficiency
Designed for safety and light weight
Fool proof locking system with an easy to use "on" and "off" lever
3 times rated capacity factor of safety to meet the safety standards as per international standards for under the hook devices
Test certificate for safety factor from government approved third party
No Maintenance and Operating cost
No damage to the work piece being lifted
Very Compact
Our Services
1.Client
We treasure and try to understand all the different needs of our clients and seek to forge a long term professional relationship with them. The satisfaction of each and every customer is our main goal and motivation in conducting our business.
2. People
We work as a team and treat each other with respect. Our solid, capable and knowledgeable team is valued as the greatest asset and an integral part of the business.
3. Product
Our products are of HIGH quality standards and always come with certificate of compliance by the manufacturers.
4. Performance
We aim to achieve high level of performance and satisfaction to both our client and people, which include delivering high quality services and treating people with integrity.
5. Free sample and OEM service
We can provide free samples to you and we also have OEM service, we can put your logo on the label and the information you need on the webbing too.
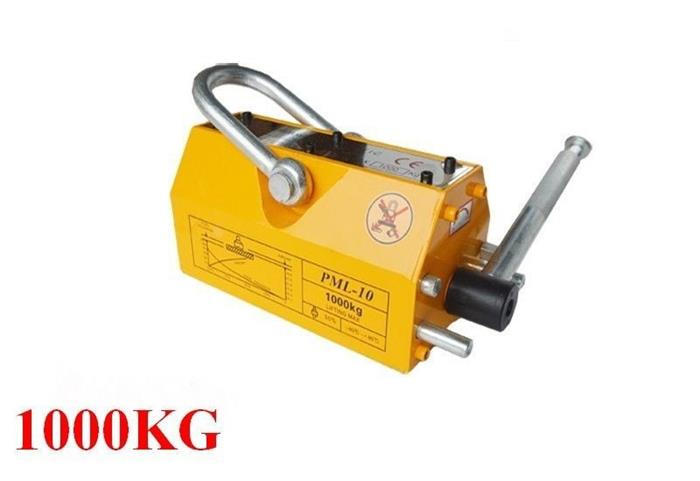
Magnetic Lifter
Magnetic Lifter,Permanent Magnet Lifter,Magnetic Hand Lifter,Magnetic Load Lifter
Hebei Liston Lifting Rigging Manufacturing Co., Ltd. , https://www.liftingriggings.com